What is VMP Brief information about Qualification, Validation and calibration of Equipment, Instrument and System. A document providing information on the company’s validation work programme. It should be define details of and timescales for the validation work to be performed. Responsibilities relating to the plan should be stated. 2.2 Which Guideline follow for preparation of VMP PIC/S (PI 006), WHO TRS 961, Eudralex Volume 4 2.3 Contents of VMP. Cover Page, Table of contents Approval of document Introduction, Objective, Scope Quality policy Validation policy Quality Risk Management Policy Responsibility Validation / Qualification Schematic Flow Validation and Qualification approach Revalidation and Requalification approach Qualification Activity Facility Qualification Qualification and Validation of Utilities Equipment Qualification Laboratory Instruments and Equipment Personnel Qualification Products and Process Validation E...
Posts
Showing posts from 2017
Requirement of Active and Passive Air Sampling in Controlled Areas
- Get link
- X
- Other Apps
Air sampling is a mandatory procedure to be followed in pharmaceuticals to produce the contamination free quality product. What would you say if I ask for the causes the most contamination of products during the manufacture of pharmaceuticals? However, air is another keysource of contaminationthat most pharmaceutical facilitiesoften ignore to take precaution from. Air samplingor air monitoring is essential for Quality Control(QC) purposes especially in companies that manufacture pharmaceutical products in controlled areas or clean rooms with filtered air.Well, what pharmacists, health care practitioners, and microbiologists refer to as air sampling can simply be defined as taking a correct measurement of the practical airborne bacteria, mold, yeast, spores and fungal cells which can be collectively referred to as bioburden in the surrounding air. The two main methods used to sample air are: 1 .Active air sampling/ monitoring 2.Passive air sampling/ monitoring 1. Active Air Sampl...
New Changes in ISO Classification of Air Cleanliness
- Get link
- X
- Other Apps

Most awaited update to ISO 14644-1 is released and it has good changes those are useful for pharmaceutical manufacturing facilities. ISO 14644 Part 1 is a useful guide to maintain the good manufacturing practices in sterile pharmaceutical manufacturing as well as the oral dosage forms. This document provides the standards for the clean room classification. Revision of the guidance was started since 2007 and its drafts are already published in 2011, 2012,2014 and 2015 but none was finalized and 1999 version was applicable and expecting a new version. Finally a 2015 version is released and following are the major changes those are made in 1999 version of the ISO 14644-1 1. Title of the ISO 14644-1 is changed from “Classification of air cleanliness” to “Classification of air cleanliness by particle concentration”. 2. The number of sampling points in the area is no longer calculated as the square root of the surface area formula but it is now taken from the table...
Activated Carbon Filter and Increase in Eficiency for Water treatment plant in pharma company..
- Get link
- X
- Other Apps
Efficiency for Water System Activated carbon filters are used for water purification in water systems and application of these filters can increase the efficiency of water system. Dheeraj shukla totalpharmasoloution.blogspot.in . Activated carbon filter is used to remove chlorine and organic matter from the water. It also removes the color and odor from the water hence the turbidity of the water is also removed. It plays an important role in water purification systems where chlorine is added for decontamination. ACF is unable to remove the microbes and hardness Activated carbon filter contains carbon particles of various sizes ranging from 10 to 50 mesh. Activated carbon is prepared from coconut shells by burning in the absence of oxygen generally in an atmosphere containing nitrogen or another inert gas. This carbon is then activated by steam or chemical methods. In steam activation, this carbon is heated at 750- 950°C in the ...
Chemical Sanitization of RO Systems
- Get link
- X
- Other Apps

Sanitization of the reverse osmosis water purification system and biofilm removal from water system. To control microbial growth, RO systems must be chemically sanitized on a regular basis. Prior to sanitation it is important to chemically clean the first-pass RO system. This will help to disrupt any biofilm that protects viable bacteria from contact with the sanitant. It also removes foulants that will react with and chemically deplete the sanitizing agent. Typically this is done in a two-step process. The first step commonly involves the use of an acid cleaner such as citric acid to remove the inorganic foulants. Next, a high-pH cleaner such as sodium hydroxide is used in order to remove organic foulants. Then the system is sanitized with one ofthe following agents: formaldehyde, hydrogen peroxide, or peracetic acid/hydrogen peroxide. It is important to consult the manufacturer of the RO system to determine the correct concentrations of the chemicals th...
Reverse Osmosis System
- Get link
- X
- Other Apps

Reverse osmosis is the best known filtration method and it is widely used in pharmaceutical water systems. This process is used to remove the particles including ions from the water. Reverse osmosis system contain a semi-permeable membrane that allows to pass the water and rejects the contaminants. In most of the reverse osmosis system it cleans the membrane it self and the process is known as crossflow. Reverse osmosis is capable to remove the salts, sugars, proteins, dyes, bacteria and other particles having the molecular weight greater than 250 daltons even viruses. The reverse osmosis process requires a force to pass the water through the membrane known as driving force. This force is applied in the form of pressure with the help of high pressure pumps. Contaminates of water are separated and collected in a tank known as concentrate. Generally the RO system recovers70-80% of feed water and this efficiency decreaseas the membrane is used.The...
Problems Associated with Pharmaceutical Cleanroom Areas
- Get link
- X
- Other Apps
Maintenance of cleanroom is a critical task and have different problems of microbial contamination. Most of the contamination occurs due to the personnel working in area. Pharmaceutical cleanroom areas are used to protect pharmaceutical products from pollutants that cause undesired contamination in pharmaceutical products to be produced. These contaminants can occur due to a number of reasons. Human being plays a significant role in producing this contamination through vital body organs such as the skin Fluids that are used to decontaminate the clean rooms can cause problems. These fluids include water, detergents, and sanitizers that do not meet the required standards. Dust contains a lot of particulate particles that produce varied effects in pharmaceutical clean room areas. Dust particles are like to have spores and bacteria that are viable . Human Beings have microflora that lives on skin surfaces and underneath. The skin plays host to almost a trillion microorgan...
Aseptic Filling Process (Media Fill) Validation Protocol in Sterile Pharmaceuticals
- Get link
- X
- Other Apps
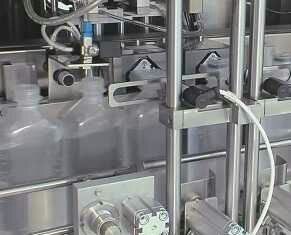
1.0 OBJECTIVE 1.1 To define procedures for validating and maintaining the validation of all aseptic filling processes and qualification of the quality of the product by system/facility/equipment. 2.0 SCOPE 2.1 This procedure applies to all aseptically filled sterile products intended for human use. 3.0 RESPONSIBILITY 3.1 The Validation personnel coordinate the aseptic filling validation program and write the sterile media aseptic filling processes reports. 3.2 Manufacturing personnel the sterile media aseptic filling processes and performs the sterile media fills. 3.3 QA personnel perform the sampling and assist with the IPQA monitoring required for each sterile media fill. 3.4 QC personnel to perform the testing and assist with the monitoring required for each sterile media fill. 4.0 ACCOUNTABILITY 4.1 Manager QA 5.0 REFERENCE (S) 5.1 In- house. 5.2Pharmaceutical Inspection convention Guidel...
Basics of HVAC System
- Get link
- X
- Other Apps

Basics of HVAC System HVAC system is a basic requirement of a pharmaceutical manufacturing facility. It has different parts those help to maintain the requiredtemperature and humidity in the manufacturing area. Air conditioning has changed over years, HVAC system is used to control the environment in the manufacturing as well as the storage area of the pharmaceutical facility. Heating, Ventilation and Air Conditioning is a system that is used to control the air temperature by controlling the air filtration and the moisture in the air. This system is used to control the temperature of a designated space with the control of the moisture in the air, supply the area with fresh air by controlling the carbon dioxide and oxygen level. It alsocontrols the contaminationof airborne particles by regulating the movement of air. The HVAC system can effectively control the air conditions of a given paramet...
Methods and Techniques Used in Effluent treatment plant and solid waste Management
- Get link
- X
- Other Apps

Pharmaceutical and biotechnology manufacturing plants discharge different types of effluents and solid wastes. These effluents and solid wastes should be handled and treated carefully because they can cause a major threat to environment and biodiversity. As these wastes contain varieties of contaminants, if they are not treated before disposal to the environment, they can cause pollution. Industrial wastes are also a cause of contamination of soils. Sludge formed in industrial process destroy vegetation and result in formation of lifeless areas on earth surfaces. According to a report of Central Board for Prevention and Control of Water Pollution (CBPCWP), 1979, the industries of Mumbai accounts for 13% of total dump into water bodies. In Kolkata, 89% of wastes are of domestic origin. In Delhi, Yamuna receives about more than 200 million of untreated human wastes while the industries account for only 20 million liters of effluent. (Trivedi, R.K. and Goel,P.K. (1984...
Duct Designing in HVAC System
- Get link
- X
- Other Apps

http://totalpharmasoloution.blogspot.in Designing an air conditioning duct system is crucial while installing HVAC system in the enclosure. An improper design of HVAC system may not give that satisfaction of the comfort level as well as it may lead to a negative impact on your energy bill. Several parameters are considered while designing the duct system for air conditioning, such as the rate of airflow, energy load, proper positioning etc. Keeping in mind that the fans are fixed, the ducts are really used as a movable (or fixed in some cases) ventilator. Numbers of designs are taken under consideration for the available space to install the duct and the requirement.General Rules for Duct Designing *.Air flow should be direct that conserves energy, space and cost altogether. *.To reduce noise, air velocity should be within permitted range. *.Quality and recommended materials should be used to construct the duct. These materials should be smoother. *.If you are changi...
Chlorination and De-chlorination of Water System
- Get link
- X
- Other Apps
Chlorination and De-chlorination of Water System Effective concentration of chlorine and chlorination and de-chlorination of water system using Sodium hypochlorite and Sodium meta bisulfite Purified water is a basic requirement of any pharmaceutical company. Generally the source of raw water remains a bore well and raw water is stored in a storage tank. This raw water is stored for several days. These storage tanks are not cleaned for many days. Due to these situation problem of microbial growth would occur in raw water storage tank and contaminate the whole water system. This is a common problem in pharmaceutical industries and generally solved by chlorination of the water storage tank. Sodium hypochlorite is used for chlorination of water. When sodium hypochlorite is dissolved in water is gives free chlorine that forms hypochlorous acid which actively takes part intensification process.Cl2+ H2O → HOCl + HCl Chlorine is a strong oxidizing agent that oxidizes organic compoun...
- Get link
- X
- Other Apps

Purified Water Storage and Distribution System Learn about the purified water storage and distribution system and procedure for validation. The purified water is prepared by purified water generation system (Reverse Osmosis System) and collected in purified water storage tank of required capacity and distributed by a centrifugal pump for loop recirculation.At different points of use separate heat exchangeris provided (if required) to bring down temperature of hot circulating water as and when required. There is a back pressure valve in the return line. Instruments and on/off valve are for controlling and monitoring the system operation and water quality. These are controlled from a centralized control panel consisting of a PLC board. The distribution piping consists of sanitary tubes, fittings, valves with orbital welding and triclover clamp in manufacturing area and for instrument connections. The water through this piping is supplied to various user points and circulated ...
Importance and Method of De-gassing in Purified Water System
- Get link
- X
- Other Apps
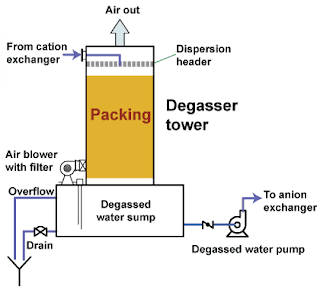
pharmawatertreatment mportance and Method of De-gassing in Purified Water System Learn how is it important to de-gas the water treated with cation bed and the procedure of de-gassing using forced draft method. In pharmaceutical industries, bore-well is the principle source of the raw water.Raw water is purified by water purification systems to use in pharmaceutical manufacturing. Cation and anion beds are used to remove the hardness of raw water Degassers are used to remove the dissolved gases from the water. When water is passed through the cation exchange, carbonates and bicarbonate ions are converted into the carbon dioxide (CO2). Carbon dioxide is soluble in water, therefore; it is not removed from the treated water.This carbon dioxide increases the ionic load on the anion bed resulting in the more consumption of the sodium hydroxide. The efficiency of the anion resin is also affected due to this dissolved carbon dioxide. Degasser should always be installed after the ...
Preparation Process for Water for Injection(WFI) in Pharmaceuticals company
- Get link
- X
- Other Apps
Water for injection is used in sterile manufacturing and its preparation and storage is a critical process. There are basically two types of water preparationin pharmaceuticals. Water for Injection (WFI) preparation process and Purified Water preparation process. The analytical standards for the two water are almost very similar, the only difference is that Water for Injection (WFI) preparation process in pharmaceuticals has stricter bacterial control standards than purified water process and has to pass the bacterial endotoxin test. Preparation methods are very similar to a particular point, however, Water for Injection (WFI) preparation process in pharmaceuticals must include distillation or double pass reverse osmosis techniques. ...